Asset Tracking: A Roll Cages Use Case
Whether it be on supermarket floors or retail delivery areas, we’ve all seen plenty of roll cages. They come with plenty of benefits, such as their strength and protection and their ability to allow stock to be transported quickly.
But there are some challenges linked to roll cages that often cost businesses money, time and productivity.
Here, we explore the benefits of roll cages and how tracking helps mitigate the challenges they can present.
Here’s the situation…
Roll cages are commonly used by post and parcel companies because they allow irregularly shaped packages to be transported quickly and without damage.
They are also often used by retailers as they allow stock to be moved quickly, without the need for pallet trucks or forklifts. These qualities make them ideal for restocking supermarket shelves and delivering stock to small convenience stores.
Their sturdy nature makes them protective and robust. However, roll cages are expensive to buy. Despite their impressive lifespan, they can cost $100s per cage.
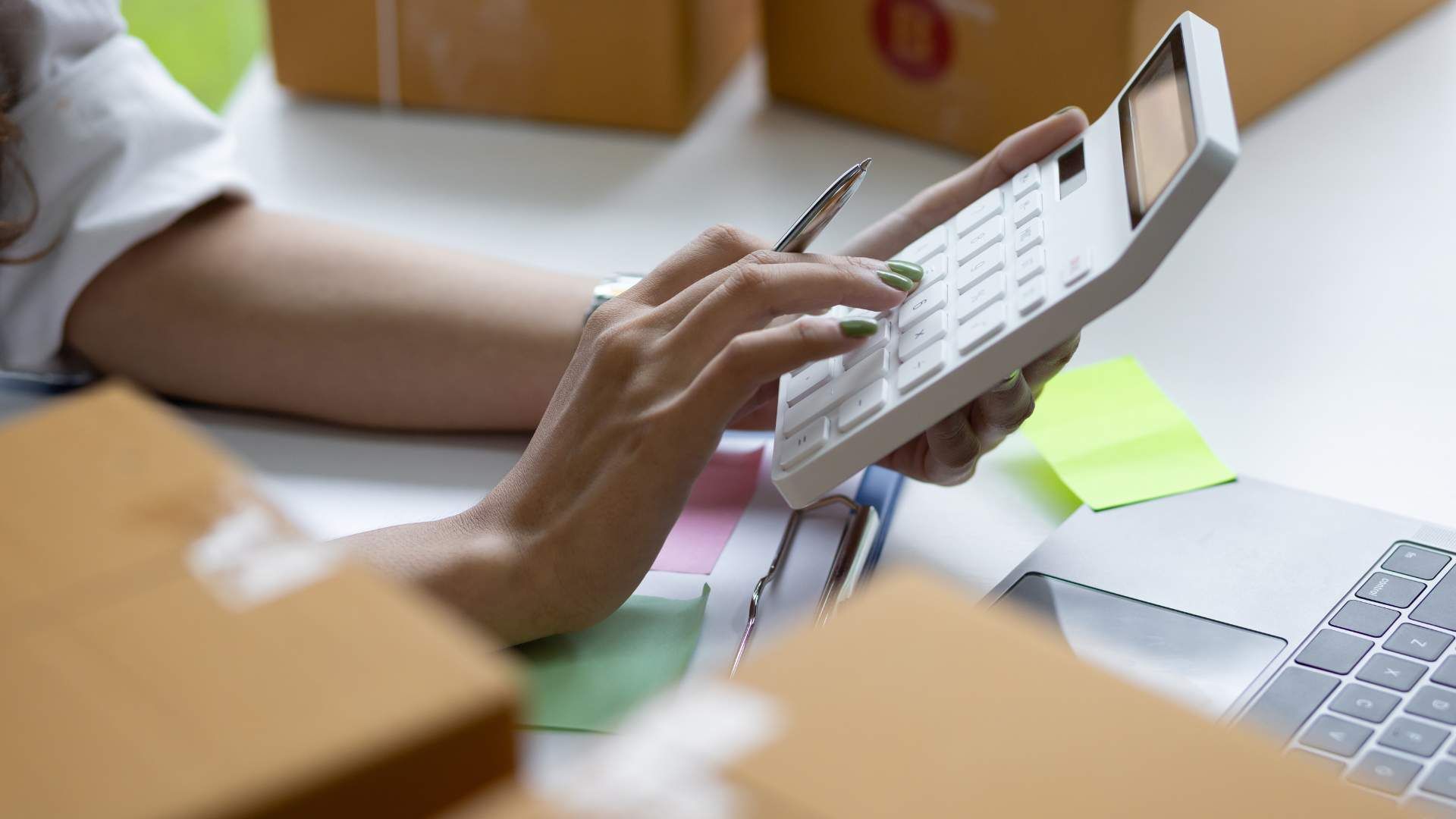
The costs
You may be thinking that, despite the hefty outlay, the long lifespan of a roll cage makes purchasing them a no-brainer. However, there are plenty of hidden costs and issues surrounding roll cages.
Upfront costs
A basic roll container could cost you $3250 or more.
Say you company runs a fleet of 5,000 roll cages. This would mean you have a valuable asset worth $1,250,000.
If you lose them at a rate of 10% each year, you’re losing $125,000. And 10% losses per year is pretty good going for non-tracked cages. Many companies are losing 50% of their untracked assets every year.
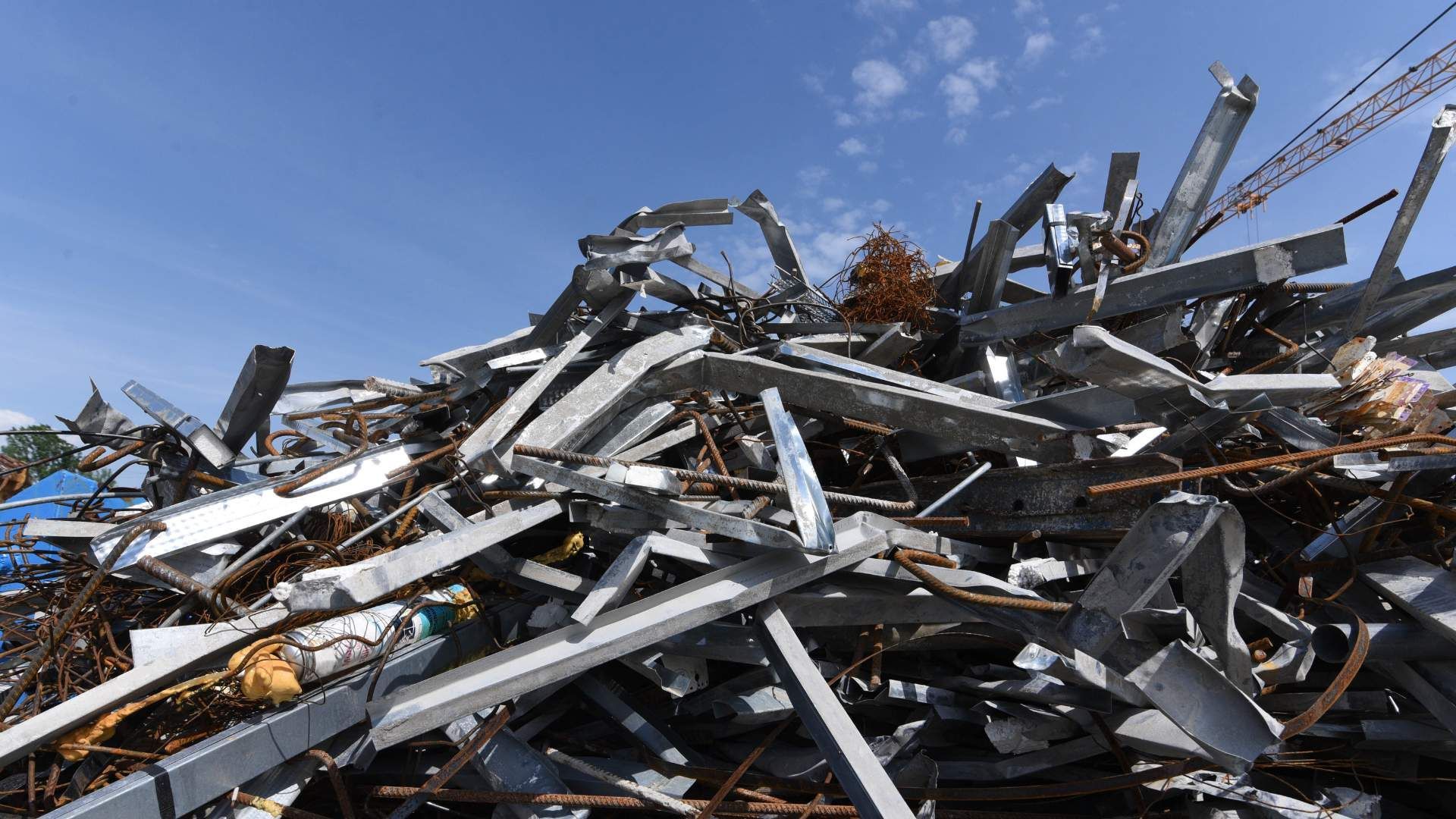
Misuse and loss
There are many reasons why roll cages are often misused or lost:
- Retailers often continue to use them rather than returning them
- Post and parcel businesses send roll cages to pick up packages but are often collected by competitors
- Roll cages are taken for scrap value, which can be significant when metal prices are high
- Roll cages are often treated simply as storage or transportation for stock, rather than a valuable asset
- Retailers and producers often hoard roll cages to avoid running out – causing disruptions across your supply chain
When roll cages are essential to a business’s processes, it’s a big problem if they’re not there.
For example, if a retailer doesn’t have enough cages to send packages for shipment, they resort to sending parcels in sacks. These sacks have to be manually unloaded, requiring additional labour and time.
One of our customers has even told us that this issue meant they were unable to meet 24-hour shipping targets, resulting in customer dissatisfaction and potential financial penalties.
How can businesses reduce losses and purchases of new cages, while avoiding shortages?
The best way to ensure roll cage management doesn’t negatively impact your processes is asset tracking.
Tracking your roll cages ensures that:
- The right number are at each location
- Shipments are not delayed due to a lack of cages
- Misuse and stockpiling issues are addressed quickly and efficiently
- Stolen and scrapped roll cages are addressed
(including unreliable locations prone to leaks and theft, scrap yards and stolen delivery vehicles)
With Sensize’s technology, assets can be tracked all over the world.
In the case shown below, all assets were intended to stay in the UK. As you can see, some roll cages were located in Ireland, France, the Netherlands, Hungary and eventually a metal scrapyard in Türkiye.
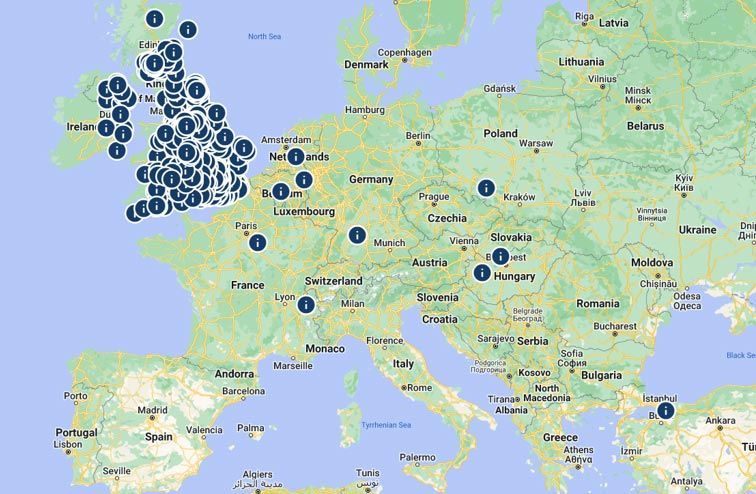
How Sensize can help
At Sensize, we have established that tracking can help alleviate the financial and productivity costs linked to roll cages.
Many different types of tracker are available on the market using a diverse range of technologies including LTE-M, NB-IoT, LoRa and Sigfox, but which one is best for tracking roll cages?
It’s important to avoid tracking systems that require the installation of access points or infrastructures onsite as these can be difficult to manage, monitor and maintain.
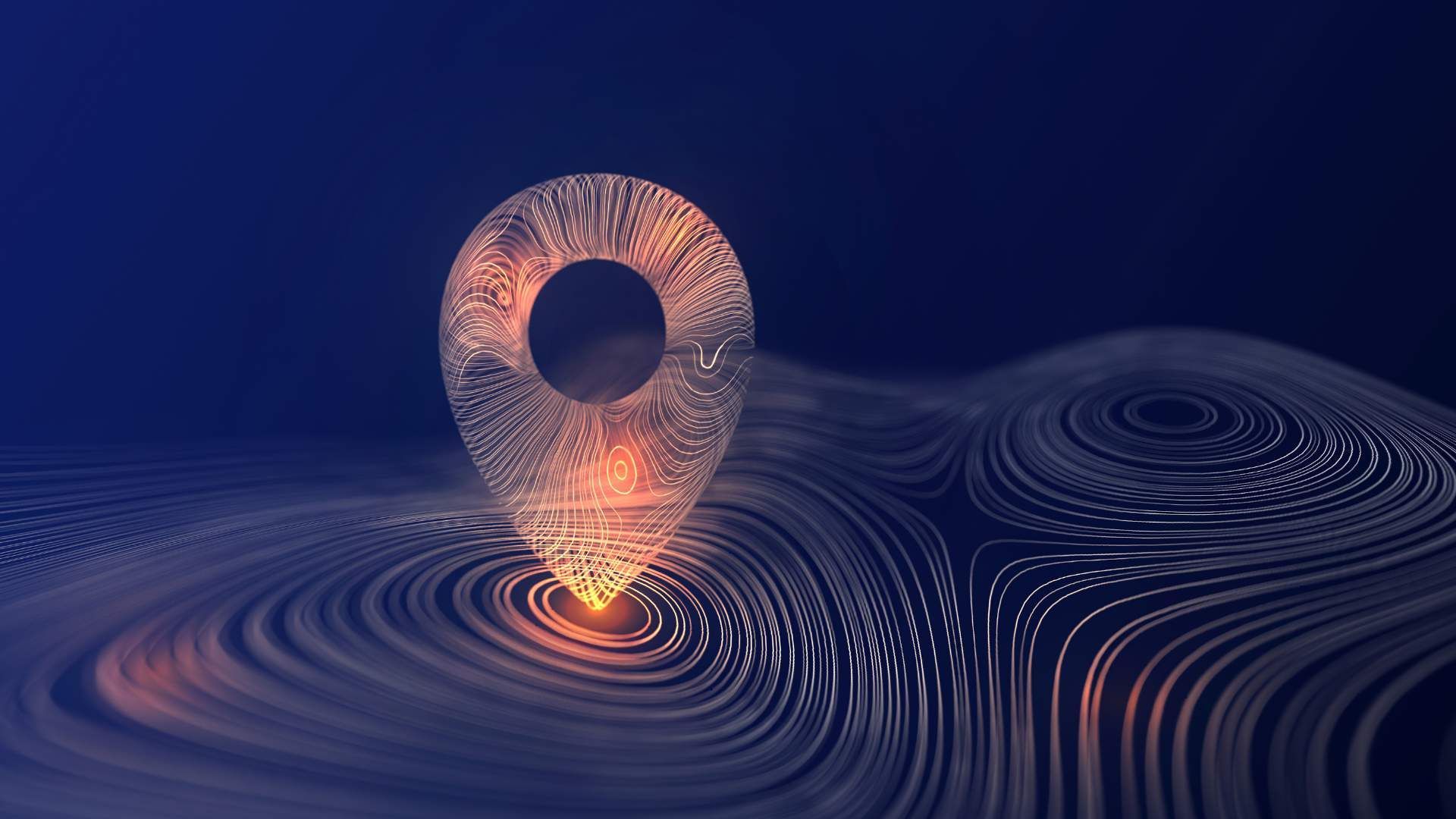
Usually, it’s best to choose a mainstream cellular networking system, such as LTE CAT1.
Here’s why:
They have the best coverage
The metal in roll cages and the goods they carry attenuate radio signals. LTE trackers use networks with strong signals and superior coverage.
They can connect to multiple operators
In most locations, there are three to five operators available – and it’s possible to enable LTE trackers to connect to any of these.
They enable international roaming
Trackers should be able to connect in multiple countries. We were able to find cages in Türkiye with effective roaming. LTE trackers have the best roaming capabilities and are supported almost everywhere.
They offer long-term support
Due to their use in many high-volume markets, LTE trackers will be around for some time. This is not the case for many esoteric technologies.
On top of this, LTE trackers are incredibly cost-effective, they are mechanically durable and their battery life matches the expected life of a roll cage, so there’s no need to worry about replacing it.
If this sounds like this suits your business, get in touch with us.
We will identify the best tracking solution for you and provide access to the Sensize Portal, enabling you to have full visibility over your assets at all times.
Share this post by clicking below...
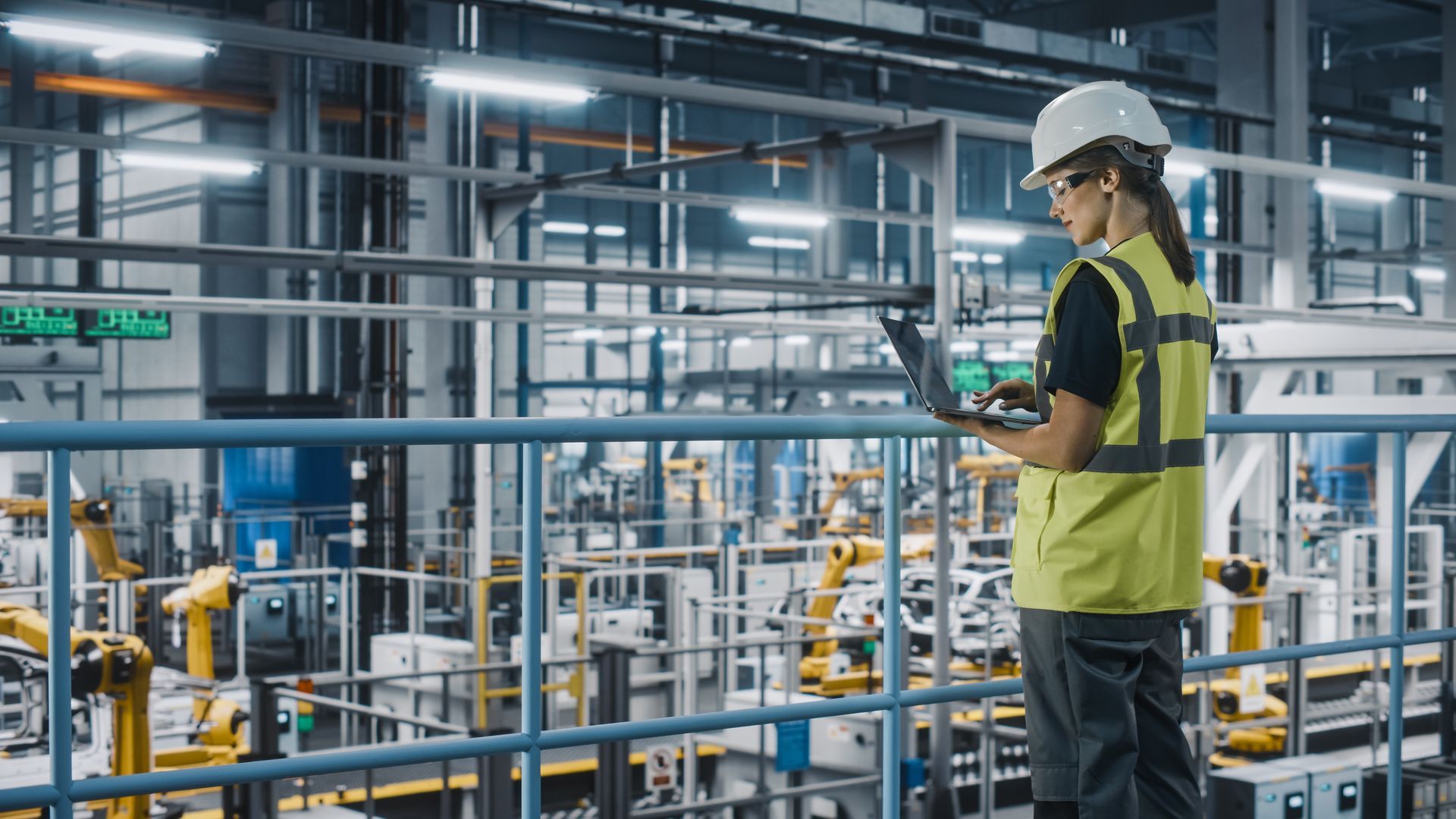
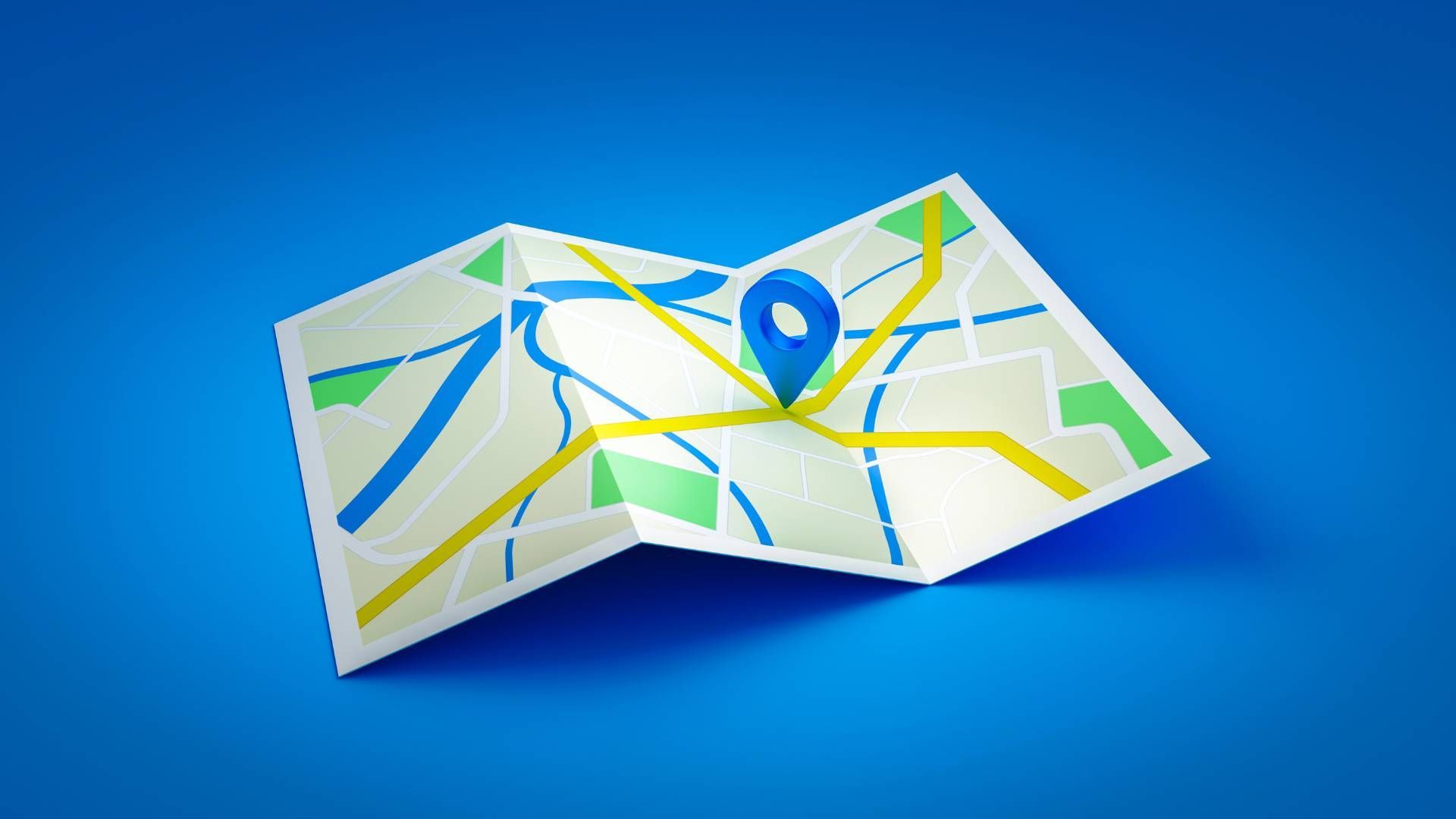
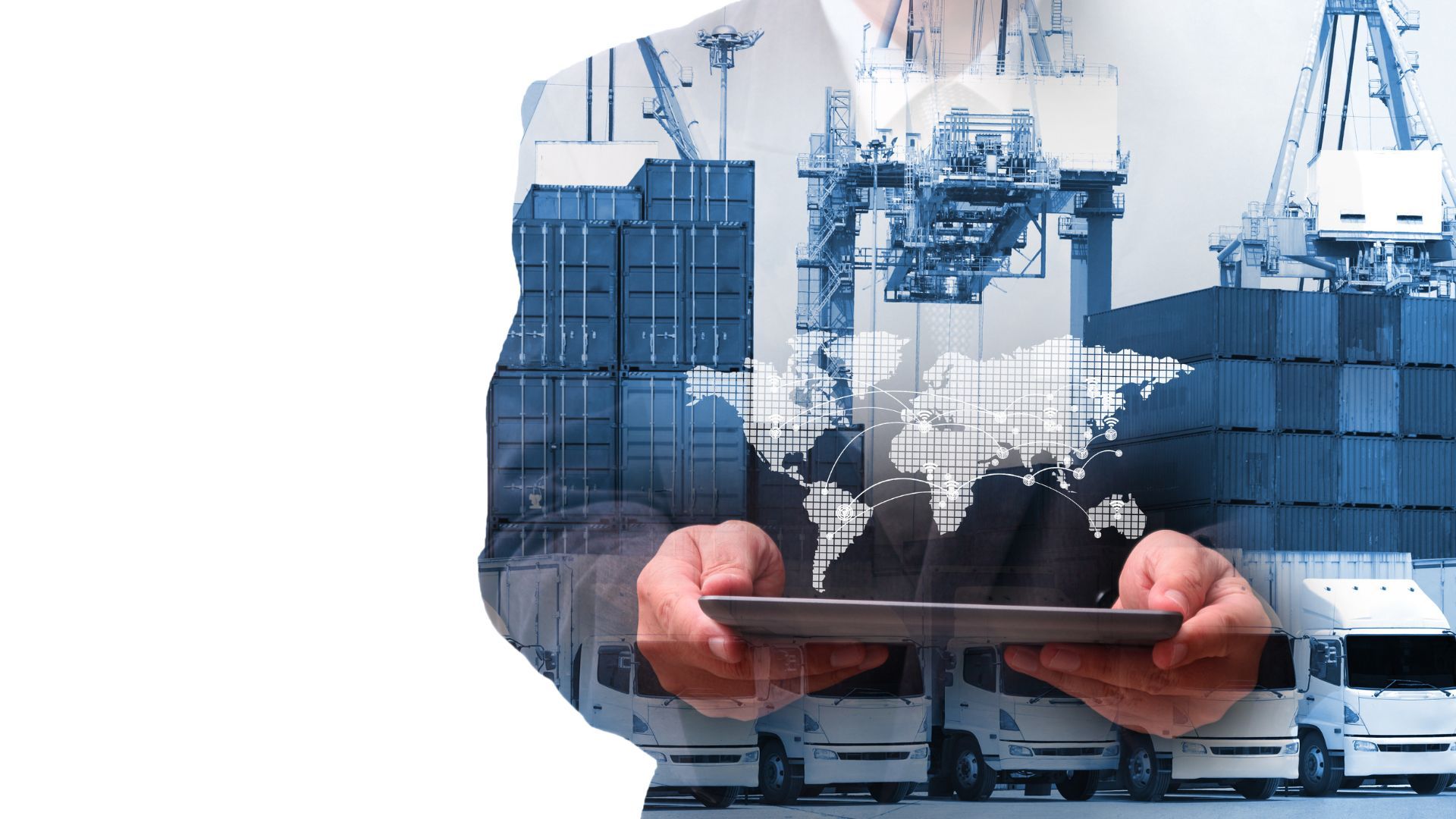